Casting and Forging Adopt Two Different Processing Techniques
Casting and Forging Adopt Two Different Processing Techniques
Aug 05, 2020
Foundry is to change shapeless molten metal into a shaped solid. A cast valve is a valve made by casting.
Forging is mainly formed by extrusion at high temperature. It can refine the grains in the manufactured parts. Forged valves are forged out.
Types of forging:
Classified by deformation temperature:
When the temperature exceeds 300-400℃ (blue brittle zone of steel) and reaches 700-800℃, the deformation resistance will decrease sharply and the deformation energy will be greatly improved. According to forging in different temperature zones, due to different forging quality and forging process, it can be divided into three types according to forming temperature zones: cold forging, warm forging and hot forging. The initial recrystallization temperature of steel is about 727℃, but 800℃ is generally used as the dividing line. Hot forging is higher than 800℃; Between 300 and 800℃, it is called warm forging or semi-hot forging. Forging at room temperature without heating is called cold forging.
When forging at low temperature, the size of forgings changes little. When forged below 700℃, the oxidation is less, and there is no decarburization on the surface. Therefore, as long as the deformation meets the forming energy, it is easy to get good dimensional accuracy and surface finish by cold forging. As long as the temperature and lubrication cooling are well controlled, the warm forging below 700℃ can also obtain good precision. During hot forging, large forgings with complex shapes can be forged because of small deformation energy and resistance. In order to obtain forgings with high dimensional accuracy, hot forging can be processed at 900-1000℃. In addition, attention should be paid to improve the working environment of hot forging. The life of forging dies (2-5 thousand for hot forging, 10-20 thousand for warm forging, and 20-50 thousand for cold forging) is shorter than that of forging in other temperature ranges, but it has a large degree of freedom and low cost.
When the billet is cold-forged, it will be deformed and hardened, which makes the forging die bear high load. Therefore, it is necessary to use high strength forging die and adopt treatment method of hard lubricating film to prevent wear and adhesion. In addition, in order to prevent the billet from cracking, intermediate annealing is required to ensure the required deformability. In order to maintain a good lubrication state, the billet can be phosphatized. At present, the cross-section can not be lubricated during continuous processing with bar and wire rod, and the possibility of phosphating lubrication is being studied.
Forging is mainly formed by extrusion at high temperature. It can refine the grains in the manufactured parts. Forged valves are forged out.
Types of forging:
Classified by deformation temperature:
When the temperature exceeds 300-400℃ (blue brittle zone of steel) and reaches 700-800℃, the deformation resistance will decrease sharply and the deformation energy will be greatly improved. According to forging in different temperature zones, due to different forging quality and forging process, it can be divided into three types according to forming temperature zones: cold forging, warm forging and hot forging. The initial recrystallization temperature of steel is about 727℃, but 800℃ is generally used as the dividing line. Hot forging is higher than 800℃; Between 300 and 800℃, it is called warm forging or semi-hot forging. Forging at room temperature without heating is called cold forging.
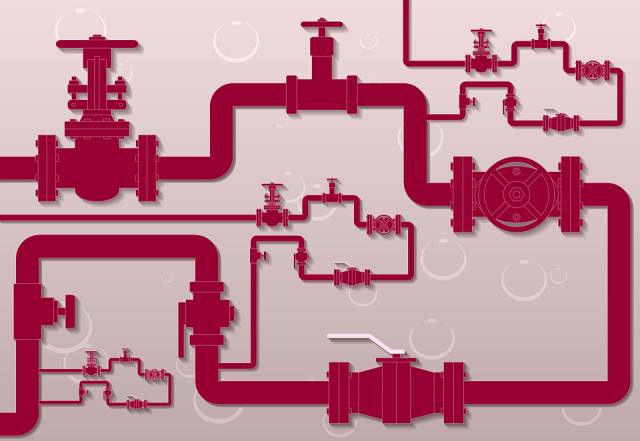
When the billet is cold-forged, it will be deformed and hardened, which makes the forging die bear high load. Therefore, it is necessary to use high strength forging die and adopt treatment method of hard lubricating film to prevent wear and adhesion. In addition, in order to prevent the billet from cracking, intermediate annealing is required to ensure the required deformability. In order to maintain a good lubrication state, the billet can be phosphatized. At present, the cross-section can not be lubricated during continuous processing with bar and wire rod, and the possibility of phosphating lubrication is being studied.
Next: Production Technology of Forged Valve
Previous: Overview of Development in Forged Flange Industry
News
About Us
Best Categories
Useful Links